20 KiB
20 KiB
Nano Hexapod - Obtained Design
Introduction ignore
Design goals:
- Position
bi
andsi
- Maximum height of 95mm
- As close as possible to "perfect" stewart platform: flexible modes at high frequency
- Easy mounting, easy change of strut in case of failure
Presentation of the obtained design:
- Fixation
- Section on: Complete strut
- Cable management
- Plates design
- FEM results
- Explain again the different specifications in terms of space, payload, etc..
- CAD view of the nano-hexapod
- Chosen geometry, materials, ease of mounting, cabling, …
- Validation on Simscape with accurate model?
Mechanical Design
<<sec:detail_design_mechanics>>
Struts
Introduction ignore
Flexible joints
Flexible joints: X5CrNiCuNb16-4 (F16Ph)
- high yield strength: specified >1GPa using heat treatment
- high fatigue resistance
Piezoelectric Amplified Actuators
APA: modification for better mounting
Encoder support
All other parts are made of aluminum.
Plates
Plates: X30Cr13
- high hardness to not deform
- Maximize frequency of flexible modes (show FEM)
- Good tolerances for interfaces with flexible joints
Positioning of
bi
and orientationsi
The cylindrical component is located (or constrained) within the V-groove via two distinct line contacts.
Finite Element Analysis
- FEM of complete system
- Show modes of the struts
Obtained Design
- Alternative encoder position: on the plates
- Support made of aluminum
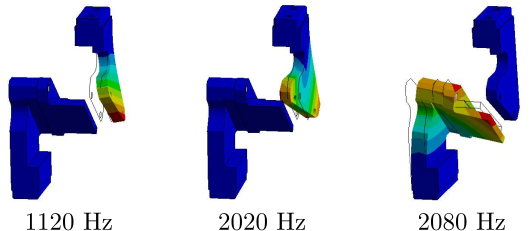
Multi-Body Model
<<sec:detail_design_model>>
Multi body Model:
- Complete model: two plates, 6 joints, 6 actuators, 6 encoders
- Joint Model
- APA Model
- Encoder model
- Say that obtained dynamics was considered good + possible to perform simulations of tomography experiments with same performance as during the conceptual design
Introduction ignore
Two configurations:
- Encoders fixed to the struts
- Encoders fixed to the plates
Flexible Joints
Amplified Piezoelectric Actuators
Encoders
Conclusion
<<sec:detail_design_conclusion>>