9.8 KiB
- Measurement description
- Static measurement of the translation stage
- Static Measurement of the spindle
#+TITLE:Static Measurements
Measurement description
Setup ignore
Setup: Each stage is statically moved of all its stroke on after the other. A metrology element is located at the sample position and its motion is measured in translations and rotations. For each small displacement, the stage is stopped and the motion of the sample is recorded and averaged.
The report by H-P van der Kleij on the static measurement of the ID31 station is available here.
Date | 2019-01-09 |
Sensors | Interferometer |
Location | Experimental Hutch |
Goal ignore
Goal: The goal here is to analyze the static measurement on the station (guiding error of each stage) and convert them to dynamic disturbances that can be use in the model of the micro-station.
Static measurement of the translation stage
<<sec:static_ty>>
ZIP file containing the data and matlab files ignore
All the files (data and Matlab scripts) are accessible here.
Notes
- 5530: Straightness Plot: Yz
- Filename:
r:\home\PDMU\PEL\Measurement_library\ID31\ID31_u_station\TY\12_12_2018\linear deviation _tyz_401_points.txt
- Acquisition date: 09/01/2019 13:49:42
- Current date: 08/03/2019 08:46:35
- Measurement Type: STRAIGHTNESS vertical
- Travel Mode: Bidirectional
- Number of Target Positions: 401
- Number of total data pairs: 2406
- Number of total data runs:6
- Position Value Units: millimeters
- Error Value Units: micrometers
Environmental Data | Min | Max | Avg |
---|---|---|---|
Air Temp (C) | 024,57 | 024,61 | 024,59 |
Air Prs (mm) | 742,56 | 743,29 | 742,83 |
Air Hmd (%) | 024,00 | 024,00 | 024,00 |
MT1 Temp (C) | 020,00 | ||
MT2 Temp (C) | 024,40 | 024,44 | 024,42 |
MT3 Temp (C) | 024,32 | 024,36 | 024,34 |
In a very schematic way, the measurement is explained on figure fig:guiding_error. The positioning error $d$ is measure as a function of $x$. Because the measurement is done in a static way, the dynamics of the station (represented by the mass-spring-damper system on the schematic) does not play a role in the measure.
The obtained data corresponds to the guiding errors.
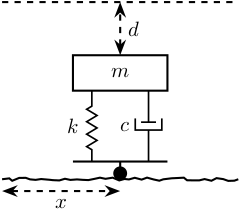
Data Pre-processing
sed 's/\t/ /g;s/\,/./g' "mat/linear_deviation_tyz_401_points.txt" > mat/data_tyz.txt
head "mat/data_tyz.txt"
Run | Pos | TargetValue | ErrorValue |
---|---|---|---|
1 | 1 | -4.5E+00 | 7.5377892E+00 |
1 | 2 | -4.4775E+00 | 7.5422246E+00 |
1 | 3 | -4.455E+00 | 7.5655617E+00 |
1 | 4 | -4.4325E+00 | 7.5149518E+00 |
1 | 5 | -4.41E+00 | 7.4886377E+00 |
1 | 6 | -4.3875E+00 | 7.437007E+00 |
1 | 7 | -4.365E+00 | 7.4449354E+00 |
1 | 8 | -4.3425E+00 | 7.3937387E+00 |
1 | 9 | -4.32E+00 | 7.3287468E+00 |
Matlab - Data Import
filename = 'mat/data_tyz.txt';
fileID = fopen(filename);
data = cell2mat(textscan(fileID,'%f %f %f %f', 'collectoutput', 1,'headerlines',1));
fclose(fileID);
Data - Plot
First, we plot the straightness error as a function of the position (figure fig:raw_data_tyz).
figure;
hold on;
for i=1:data(end, 1)
plot(data(data(:, 1) == i, 3), data(data(:, 1) == i, 4), '-k');
end
hold off;
xlabel('Target Value [mm]'); ylabel('Error Value [$\mu m$]');
<<plt-matlab>>
Then, we compute mean value of each position, and we remove this mean value from the data. The results are shown on figure fig:processed_data_tyz.
mean_pos = zeros(sum(data(:, 1)==1), 1);
for i=1:sum(data(:, 1)==1)
mean_pos(i) = mean(data(data(:, 2)==i, 4));
end
figure;
hold on;
for i=1:data(end, 1)
filt = data(:, 1) == i;
plot(data(filt, 3), data(filt, 4) - mean_pos, '-k');
end
hold off;
xlabel('Target Value [mm]'); ylabel('Error Value [$\mu m$]');
<<plt-matlab>>
Translate to time domain
We here make the assumptions that, during a scan with the translation stage, the Z motion of the translation stage will follow the guiding error measured.
We then create a time vector $t$ from 0 to 1 second that corresponds to a typical scan, and we plot the guiding error as a function of the time on figure fig:time_domain_tyz.
t = linspace(0, 1, length(data(data(:, 1)==1, 4)));
figure;
hold on;
plot(t, data(data(:, 1) == 1, 4) - mean_pos, '-k');
hold off;
xlabel('Time [s]'); ylabel('Error Value [um]');
<<plt-matlab>>
Compute the PSD
We first compute some parameters that will be used for the PSD computation.
dt = t(2)-t(1);
Fs = 1/dt; % [Hz]
win = hanning(ceil(1*Fs));
We remove the mean position from the data.
x = data(data(:, 1) == 1, 4) - mean_pos;
And finally, we compute the power spectral density of the displacement obtained in the time domain.
The result is shown on figure fig:psd_tyz.
[pxx, f] = pwelch(x, win, [], [], Fs);
pxx_t = zeros(length(pxx), data(end, 1));
for i=1:data(end, 1)
x = data(data(:, 1) == i, 4) - mean_pos;
[pxx, f] = pwelch(x, win, [], [], Fs);
pxx_t(:, i) = pxx;
end
figure;
hold on;
plot(f, sqrt(mean(pxx_t, 2)), 'k-');
hold off;
xlabel('Frequency (Hz)');
ylabel('Amplitude Spectral Density $\left[\frac{m}{\sqrt{Hz}}\right]$');
set(gca, 'XScale', 'log'); set(gca, 'YScale', 'log');
<<plt-matlab>>
TODO Static Measurement of the spindle
<<sec:spindle_static>>
ZIP file containing the data and matlab files ignore
All the files (data and Matlab scripts) are accessible here.